Socket Weld Flange
Socket weld flange simplified as SW flange, it has a recessed area (like a shoulder) in the flange bore, this shoulder serves as a guide to set the depth of the pipe that inserted to the flange. Socket welding flange initially designed for high pressure small diameters piping system.
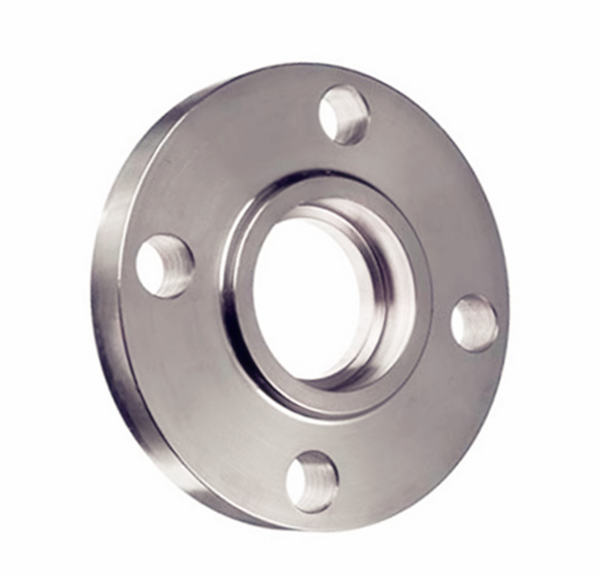
Available Material:
Standard:
Carbon steel ASTM A105, ASTM A350 LF1/2, ASTM A181
Alloy steel ASTM A182 F5, F9, F11, F22, F91
Stainless steel ASTM A182 F304/L, F316/L
Outer Diameters: 1/2 inch to 24 inch, up to 2500#
Special made: 24'' to 60'', up to 900#
Wall Thickness: Schedule 40 to 160
Pressure Ratings: Class 150 to Class 2500
Face Type: RF, RTJ
How to Use
Insert the pipe end into socket weld flange, until the pipe bottom touch the shoulder area, pull back 1.6mm (1/16'') distance of the inserted pipe then do fillet welding. The point is to create a expansion gap (1 fillet weld) between the flange and the pipes or fittings.
How is Socket Welding Flange Generated
The socket welding flange was firstly to use for stainless steel superheater, due to avoid cracking defects caused by thermal stresses in heating processes, and after years development it became a standard applications for all types of material.
Socket Welded Flange Face Types
Socket welded flange inlcuding RF type and RTJ type, which like other types of welding flanges (slip on, weld neck or blind flange).
RF Type
RF socket weld flange has a small portion surrounding the flange bore that protrudes from the face. Gasket seat will be placed in this raised area.
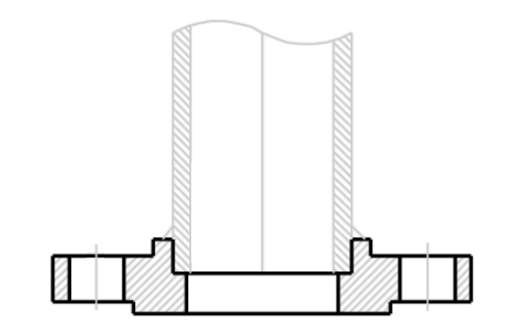
RTJ Type
On the raised face surface there has a groove is RTJ type, which you can place a gasket ring to get better sealing performances.
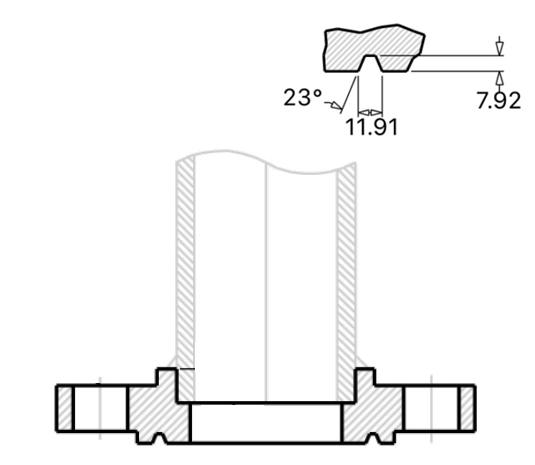
Advantages
- Socket weld flange could replace threaded flange, to minimize the risky of leakage.
- No need to beveling before welding.
- Welding work outside of the pipe, will not penetrate the pipe bore
- It is recommended for applications where internal welding operations are particularly difficult. This sock welded construction eliminates internal pockets while avoiding warpage of welding heat and damage to the flange face caused by weld spatter. It has the same internal pressure as the sliding on the flange, and has a better fatigue life.
Disadvantages:
- Socket welded flange requires higher skills for welder, which the welding need to make sure that the expanding gap between the pipe and shoulder is 1/16 inch.
- The expansion gap create the chances for the crack defects, especially for anti corrosive pipes as stainless steel pipes, so the cracks between the pipe and flange will cause the corrosive problems. So SW flange will not be compatible with corrosive or radioactive environment, as this solid buildup at the joint can cause operational and maintenance problems. So that's why people use but welding more often as the welding completely through the pipe from outside to inside, which makes the connects more strong and anti corrosive.
Socket Weld Flange vs Slip On Flange
Socket welded flange shape is similar to slip on flange, differently it has a shoulder at the inner bore.
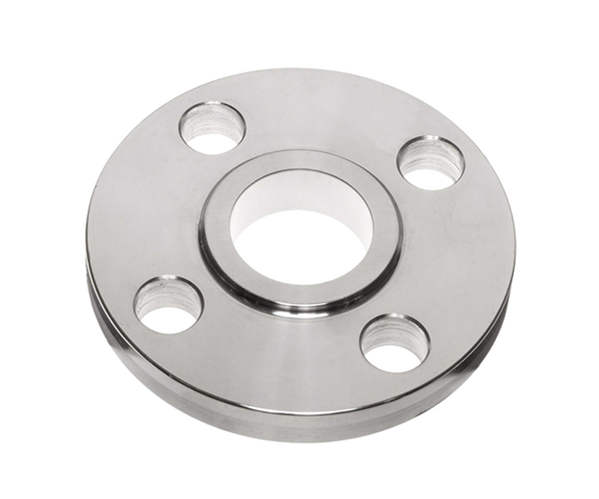
Slip On Flange - No shoulder at inner bore.
Socket weld flange static strength is equal to slip on flange, but it's fatigue strength is 50% higher than the double welded slip on flange.