Slip On Flange
Slip on flange, also called SO flange. It's a kind of flange slides over the pipe with internal design is slightly larger than the pipe. Since the inner diameter of the flange is slightly larger than the outer diameter of the pipe, that is designed to slide over the end of a pipe. The SO flange can be directly connected to equipment or pipe by fillet weld at the top and bottom of the flange. It is used to insert the pipe into the inner hole of the flange.
Here are some key features and characteristics of slip-on flanges:
Key Features of Slip-On Flanges:
- Design:
- Slip-on flanges have a flat face and are typically welded to the pipe after being slipped over it. This design allows for easy alignment and installation.
- Installation:
- They are easier to install compared to other flange types, as they do not require precise alignment of the pipe ends. The flange can be positioned and then welded in place.
- Applications:
- Slip-on flanges are commonly used in low-pressure applications and are suitable for various industries, including oil and gas, water treatment, and chemical processing.
- Cost-Effectiveness:
- Generally, slip-on flanges are more cost-effective than other types of flanges, such as weld neck flanges, due to their simpler design and installation process.
- Material:
- They can be made from various materials, including carbon steel, stainless steel, and other alloys, depending on the application requirements.
- Limitations:
- While slip-on flanges are versatile, they may not be suitable for high-pressure applications due to the potential for leakage at the weld joint.
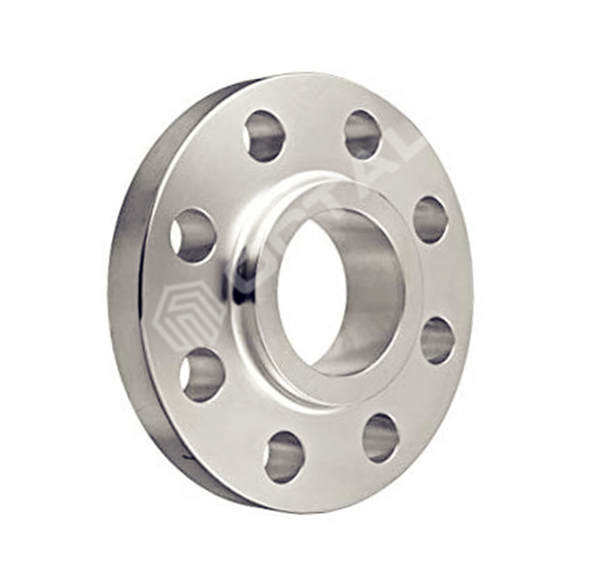
Our Supply Range:
Standard: ASTM A105, ASTM A182
Material: Carbon Steel, Alloy Steel, Stainless Steel
Size: 1/2'' to 24'', customized up to 60''
Pressure Ratings: Class 150 to Class 2500
Face Type: RF, RTJ
Types of Slip On Flange Welding
The slip-on (SO) flange can be classified into two types: SO welding plate flanges and SO welding hubbed steel pipe flanges. Its mechanical properties fall between those of integral flanges and loose flanges. The design is straightforward, and the manufacturing process is easy, making slip-on flange welding a popular choice for various fluid pipelines.
Based on different face types, there are also raised face types and ring joint face types available.
Raised Face Slip On Flange
A raised face slip-on flange features a small protrusion on its bottom face. This raised area is designed to accommodate a gasket during installation, enhancing sealing performance.
As the pressure ratings increase, the height of this raised face also increases.
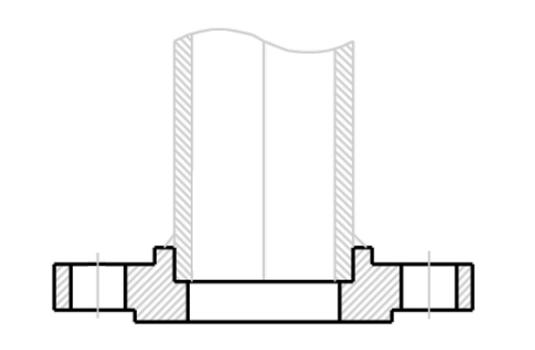
RTJ Slip on Flange
A small grooved is machined on the raised face part, this form is called RTJ type, the function of this groove is to place the gasket ring, also applied for sealing, compared to RF type, RTJ is designed for high pressure use.
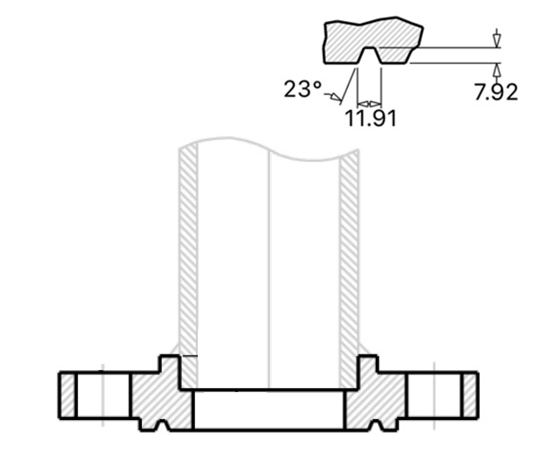
Slip on flange use slip welding to connect equipment, so either below of name is describing the same flange:
- Slip on weld flange
- Slip on flange weld
- Weld slip on flange
- Slip on flange welding
- SO flange
Referred Standard and Grades
ASTM A105 for carbon steel slip on pipe flanges.
ASTM A182 for alloy and stainless slip on flanges. (Alloy for F11, F22, stainless for F304/F304L, F316/F316L)
ASME B16.5 for pipe flanges and flanged fittings.
BS 3293
DIN 86029
Dimensions and Pressure Ratings
Common outer diameters: 1/2'', 2'', 3'', 4'', 6'', 8'', 10'', 12'', to 24”.
Special made outer diameters: Up to 60”.
Class range: Class 150, Class 300, 400, 600, 900, 1500, 2500(# or LB). PN 2.5 to PN 250.
Flange face type: RF (Raised Face), RTJ (Ring Type Joint)
Manufacturing Types
Slip-on flanges can be produced through various methods, including forging, steel cutting, and casting. Among these manufacturing processes, forged flanges offer the highest quality and are the most commonly used, although they are priced higher than other types. Therefore, it's essential to understand the specific working environment before purchasing a slip-on flange.
Advantages of Slip On Flange
- Lower installation costs
- More easy to align with other parts during installation
- Better leaking proof
- Inner and outer welding on flange
- Takes less time to cut accurately for the pipelines
- As pipe slides on the flange, it compatible with lower hub on slip on flange
Slip On Flange vs Weld Neck Flange
- The strength for internal pressure of Slip On Flange is two-thirds of Weld Neck Flange.
- Durability life is 1/3 of WN flange.
- 2 fillet welding required for SO flange, one inside and one outside of flange.
- A space shall be reserved between the end of the pipe and the end of the flange during welding work, to avoid damage the flange face.
- Slip on flange has to connect with a pipe firstly, then connect a fitting. (Combination of flange+elbow, or flange+tee not available, since the fittings not in a straight end, it can not slide completely into the flange bore. )
Slip on flange are usually cheaper than Weld-Neck flange (welding neck flange), which is why many customers prefer to choose them. It is one of the commonly used flanges for low pressure, medium temperature piping system.
On the other hand, since the flange bore is larger than the pipe diameter, it usually requires more welding work than the other flanges. So the durability is not as long as the welding neck flange, all of these factors should be considered before choose a right flange.