Blind Flange
Blind flange is like a flange cover, also called blind disk or flanged pipe plug. Blind flange has no holes in the center, for to seal the pipe opening. So it's function is the same as the pipe plug or the pipe cap. The difference is blind flange is a detachable equipment, easy to replace or do maintenance. It is essentially a solid disk that is bolted to the end of a pipe, preventing the flow of fluids or gases. Here are some key points about blind flanges:
Key Features of Blind Flanges:
Purpose:
- Blind flanges are used to close off the ends of pipes, valves, or other equipment, providing a secure seal.
Design:
- They are typically flat and have no central opening, which distinguishes them from other types of flanges that allow for flow.
Material:
- Blind flanges can be made from various materials, including carbon steel, stainless steel, and alloy materials, depending on the application and environmental conditions.
Applications:
- Commonly used in oil and gas, chemical processing, water treatment, and other industrial applications where a secure closure is needed.
Installation:
- Blind flanges are bolted to the piping system, and gaskets are often used to ensure a tight seal and prevent leaks.
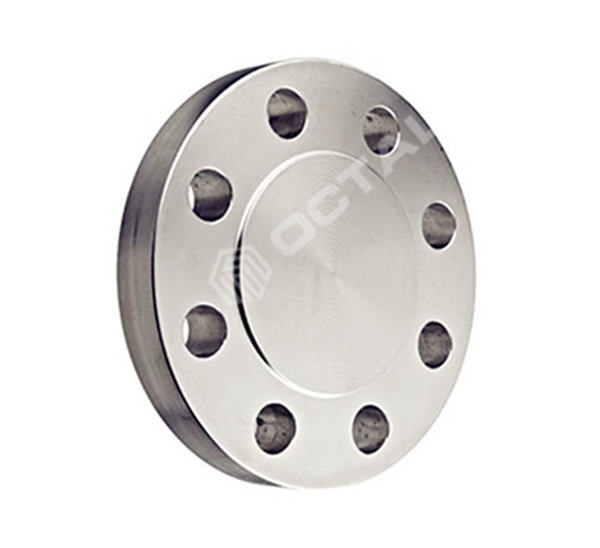
Our Supply Range
Material: Carbon, Alloy and Stainless Steel
Standards: ASTM A105, ASTM A182
Sizes: 1/2'' to 24'', Customized up to 48''
Thickness: Schedule 10(S) to SCH 160
Pressure Ratings: Class 150 to 2500
Face Type: RF, RTJ
Major Function - Where to use
The main function of a blind flange is to completely isolate the production medium. This prevents the shut-off valve from closing tightly, which can impact production and potentially lead to accidents.
Blind flanges should be installed in locations that require isolation, such as at equipment nozzles, between the front and rear of shut-off valves, or between two flanges. It is often recommended to use a figure 8 blind flange in these situations. For single-use applications like pressing and purging, a standard round blind flange is typically used.
Sealing Surface
There are several types of sealing surfaces, including flat, convex, concave, grooved surfaces, and ring joint surfaces.
Material Types and Standards
Blind Flange material usually required in carbon steel, stainless steel, alloy steel, copper, aluminum and etc.
Carbon steel blind flange: ASTM A105
Alloy steel: ASTM A182 F5, F9, F11, F22, F91
Stainless steel blind flange: ASTM A182 F304/L, F316/L
Manufacturing Standards
ASME B16.5
BS 3293
DIN 86029
Dimensions
General use OD range: 1/2'', 2'', 3'', 4'', 6'', 8'', 10'', 12'', to 24”.
Special made OD: Up to 60”.
Class range: Class 150, Class 300, 400, 600, 900, 1500, 2500
Flange face type: RF (Raised Face), RTJ (Ring Type Joint)
Manufacturing Types and Costs
There are generally four types of manufacturing processes: forging, casting, cutting from medium plates, and casting combined with forging. Among these, forging products have the highest price, followed by medium plate cutting. Casting combined with forging is less expensive, while casting is the least favorable process.
In terms of quality, forging and medium plate cutting produce the best results, while casting combined with forging is of slightly lower quality.
Casting Blind Flange
The shape of the casting flange blank is precise, requiring minimal processing capacity, making it cost-effective. However, it may have casting defects such as air holes, cracks, and inclusions. Additionally, the internal flow characteristics of the casting are poor, and if it involves cutting, the flow characteristics are even worse.
Forging Blind Flange
Forged blind flanges generally have a lower carbon content compared to cast flanges, making them less prone to rust. They also have a better streamlined shape, a denser structure, and superior mechanical properties compared to cast flanges.
However, if the forging process is not performed correctly, it can result in large or uneven grain structures and the potential for hardening cracks. Additionally, the cost of forged flanges is higher than that of cast flanges.
Overall, forged flanges can withstand greater shear and tensile forces than their cast counterparts.
Precautions When Use
- Under the premise of meeting the process requirements, use as few blind plates as possible.
- The blind plate set must be marked as normally open or normally closed.
- The location of the blind plate is determined by the cutting effect, safety and process requirements.